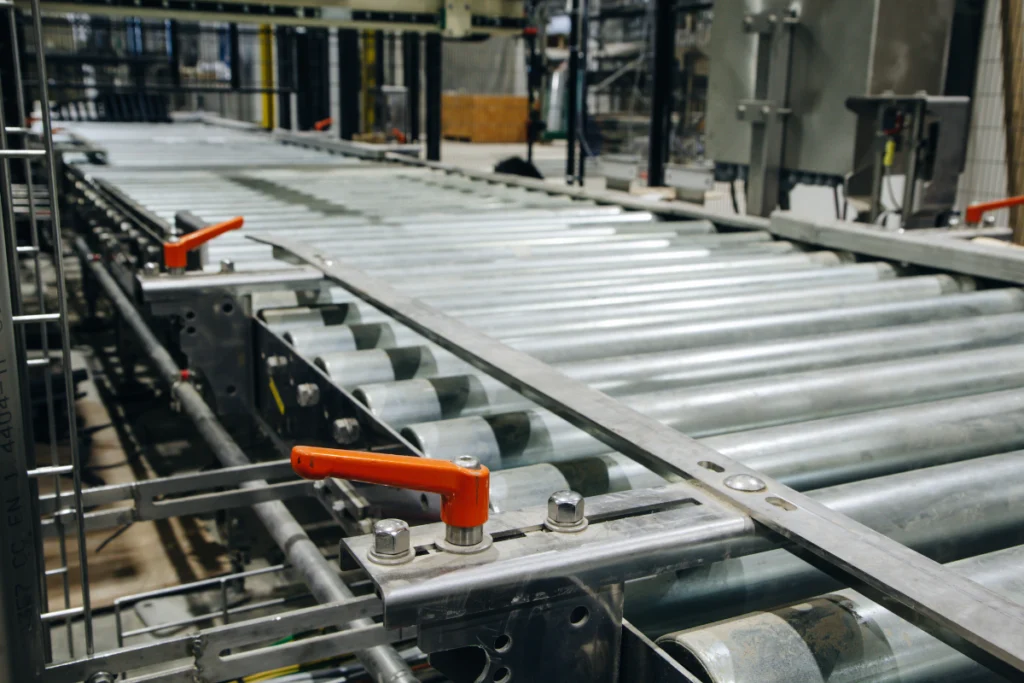
Common mistakes when selecting conveyor rollers and how to avoid them
Reading time: < 5 minutesThe proper selection of conveyor rollers is crucial to ensure operational efficiency and reduce costs in any industrial environment. A mistake in choice can lead to problems such as increased maintenance, reduced equipment lifespan, and, in the worst-case scenario, failures that halt production. In this article, we will look at some of the most common mistakes made when selecting conveyor rollers and provide practical advice on how to avoid them.
Understanding conveyor rollers
Conveyor rollers are essential components in the metalworking industry, used to facilitate the movement of materials and products throughout various stages of the manufacturing process. These rollers can vary in size, material, and design, making them adaptable to a wide range of industrial applications.
Types of conveyor rollers available
There are several types of conveyor rollers, including gravity rollers, motorized rollers, and special ones, such as adjustable or coated rollers for handling delicate materials. Each type has its own applications and advantages, depending on the specific needs of the operation.
- Gravity Rollers: Used in conveyor systems where gravity drives the movement of products.
- Drive Rollers: Equipped with internal motors, they are ideal for systems that require precise control of speed and direction.
- Tapered Rollers: Designed for curves in conveyor systems, they allow for efficient handling of products in non-linear paths.
- Coated Rollers: Covered with materials like rubber or PVC, providing increased friction and making them suitable for delicate products or slippery surfaces.
Common mistakes in conveyor roller selection
Choosing the right conveyor rollers is essential to ensure the efficiency and longevity of the conveyor system. Below, we outline some common mistakes and how to avoid them.
Ignoring the operating environment
One of the most common mistakes is failing to consider the environment in which the rollers will operate. Factors such as temperature, humidity, exposure to chemicals, and abrasion can significantly affect the performance and durability of the rollers.
Choosing based solely on cost
Selecting conveyor rollers based only on their initial cost can lead to higher expenses in the long run. Lower-priced rollers may not be suitable for certain applications, leading to premature failures and increased maintenance and replacement costs.
Lack of understanding of material specifications
Not understanding the specifications of the material being transported, such as its weight, size, and physical properties, can lead to the selection of inappropriate rollers. This can result in jams, material damage, and reduced system efficiency.
How to correctly choose conveyor rollers
To avoid the mistakes we’ve mentioned, it’s crucial to take a meticulous and well-informed approach when selecting conveyor rollers.
Detailed evaluation of the operating environment
Before selecting the rollers, it is important to assess the operating environment. This includes considering factors like temperature, humidity, exposure to chemicals, and abrasion. Choosing appropriate materials and designs for these factors can prolong the lifespan of the rollers and improve system performance.
Consult with experts
Working with experts in conveyor rollers can provide recommendations and ensure that your selection meets the specific needs of the application. Specialists can help identify the most suitable rollers based on their experience and technical knowledge.
Prioritize quality and adaptability
Quality ensures greater durability and performance, while adaptability allows for system adjustments and improvements without the need for frequent replacements. Therefore, investing in high-quality rollers that can adapt to operational variations will be essential.
Case studies and practical examples
Reviewing case studies and practical examples of similar applications can give you clear insight into which types of rollers have been effective under similar conditions. Learning from others’ experiences can help avoid costly mistakes.
At Roltia (Eurotransis), we specialize in the manufacturing of conveyor rollers, offering high-quality solutions.