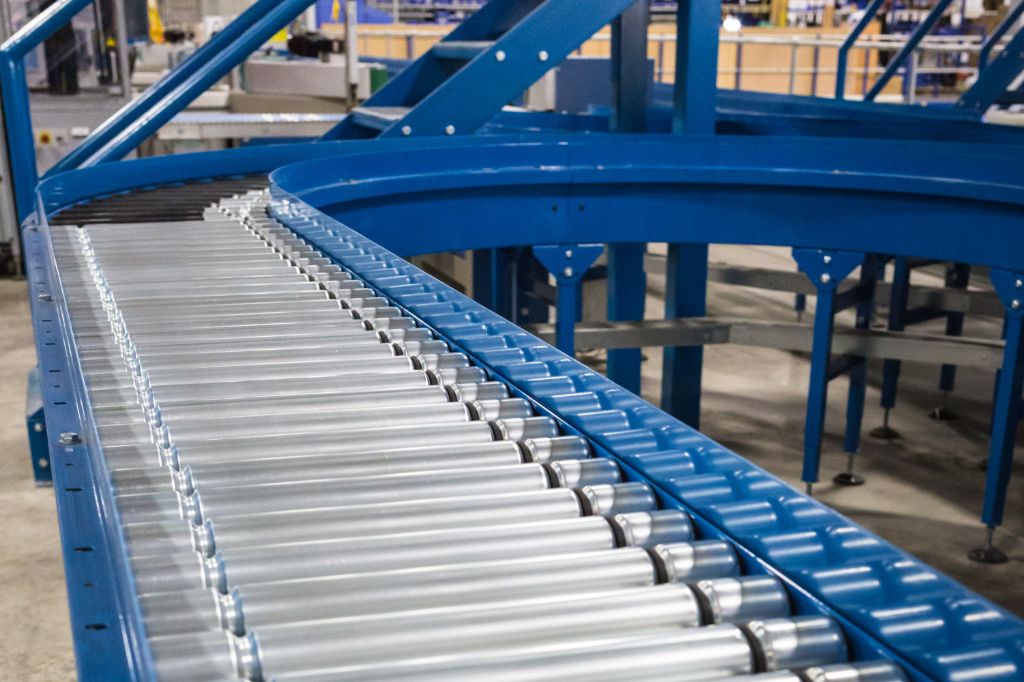
Comment Réduire le Temps d’Inactivité dans les Systèmes de Convoyeurs
Temps de lecture: < 6 minutesLe temps d’inactivité, également appelé downtime, est l’un des principaux défis pour maintenir la productivité et l’efficacité opérationnelle..
Ce phénomène peut entraîner des coûts élevés et nuire à la chaîne d’approvisionnement. Dans cet article, nous discuterons des conséquences du downtime dans la logistique, des stratégies clés pour le minimiser et des technologies émergentes qui permettent de détecter les pannes avant qu’elles ne deviennent des problèmes majeurs.
Conséquences du Temps d’Inactivité dans la Logistique
Le temps d’inactivité affecte non seulement la production, mais aussi la chaîne d’approvisionnement. Les principales conséquences sont:
- Pertes économiques : Chaque minute où un système de convoyeur reste inactif signifie moins de produit transporté et donc des revenus inférieurs. Dans des secteurs comme l’exploitation minière ou la fabrication, ces pertes peuvent rapidement augmenter.
- Retards de livraison: Un downtime non planifié peut provoquer un effet domino qui affecte les clients finaux et ternit la réputation de l’entreprise.
- Coûts de réparation imprévus : Les pannes soudaines peuvent nécessiter des réparations d’urgence, qui sont souvent beaucoup plus chères que l’entretien programmé.
- Impact sur la motivation de l’équipe : La fréquence de ces arrêts et la précipitation pour les résoudre peuvent créer un environnement de stress et de frustration parmi les travailleurs.
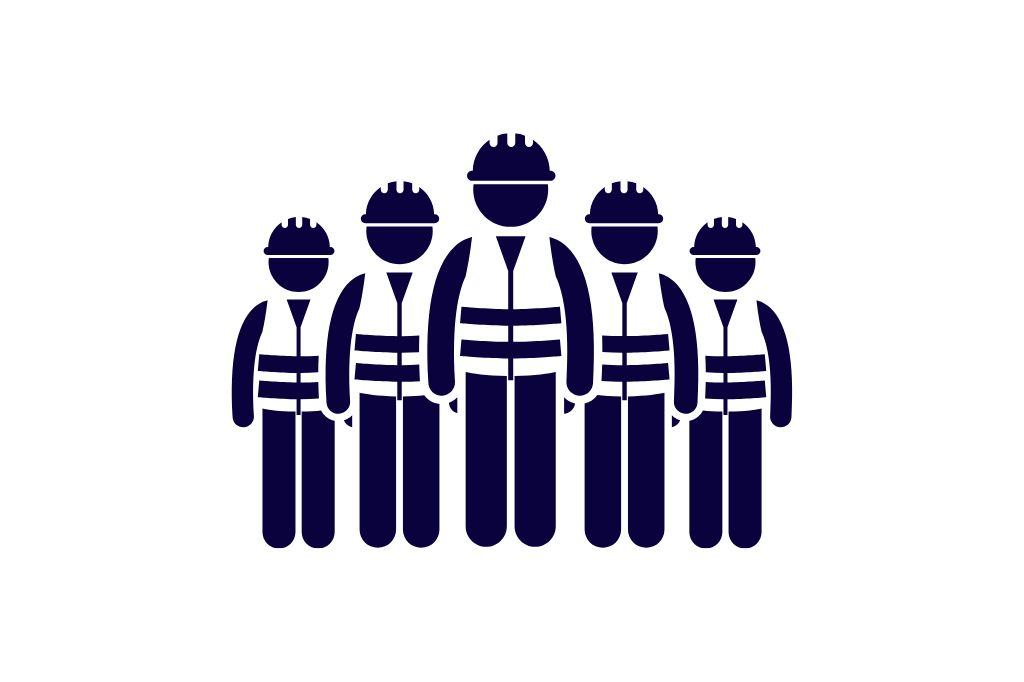
Stratégies pour Minimiser le Downtime dans les Convoyeurs
Réduire le temps d’inactivité nécessite une approche proactive et bien planifiée. Certaines des stratégies les plus efficaces sont:
- Maintenance préventive : Planifier une maintenance régulière est l’un des meilleurs moyens d’éviter des problèmes majeurs. Cela implique de vérifier régulièrement l’équipement pour identifier et résoudre d’éventuelles pannes. Un programme de maintenance préventive garantit que chaque partie du système de convoyeur est dans des conditions optimales, réduisant le risque d’arrêts imprévus.
- Formation du personnel : Il est essentiel de s’assurer que le personnel de maintenance soit correctement formé pour détecter et résoudre les problèmes. Souvent, les petites pannes peuvent être rapidement résolues si les travailleurs connaissent bien l’équipement. De plus, un personnel bien formé peut suivre des procédures d’urgence efficaces en cas de problème majeur.
- Stockage des pièces de rechange : L’accès aux pièces de rechange clés disponibles peut réduire considérablement le temps de réparation. Identifier les pièces qui ont tendance à s’user ou à se casser fréquemment et s’assurer de les avoir en stock
- Établissement de protocoles de réponse rapide : Il s’agit d’avoir un plan d’action spécifique pour chaque type de panne pouvant survenir, avec des instructions précises pour que le personnel de maintenance ou les opérateurs agissent immédiatement.
- Surveillance constante : Cela aide à identifier des modèles ou des problèmes récurrents. Cela peut être réalisé par des inspections régulières ou via des technologies de capteurs permettant de collecter des données en temps réel, comme indiqué dans la section suivante.
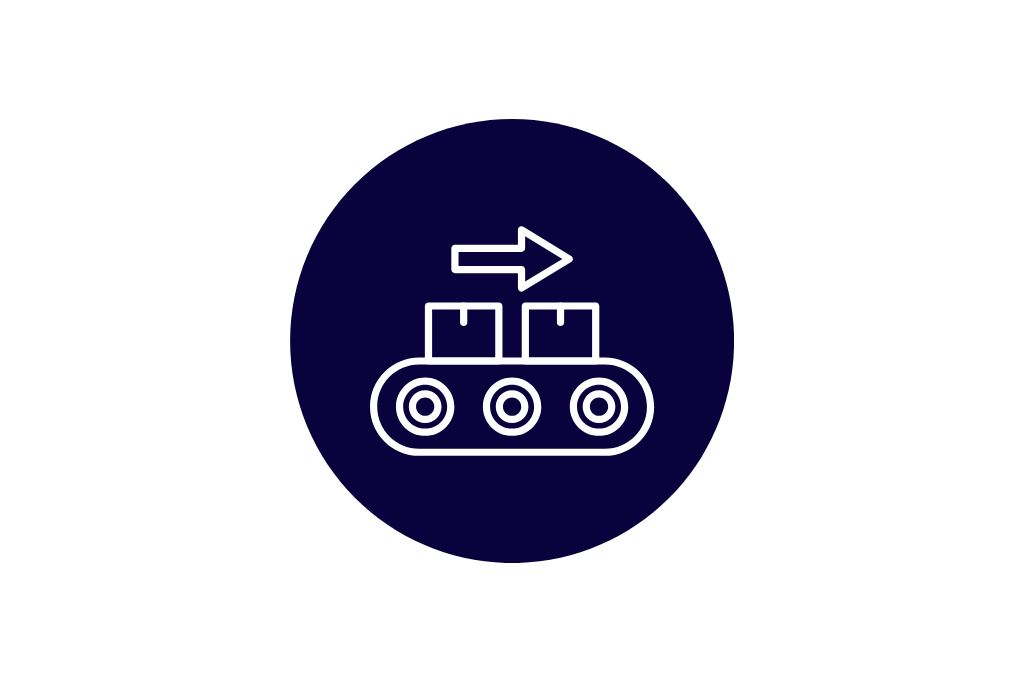
Technologie de détection précoce des pannes
Avec l’avancement de la technologie, des outils émergent permettant de prévenir les pannes potentielles, ce qui conduit à une maintenance plus efficace et à un moindre impact opérationnel. Certaines de ces technologies comprennen:
- Capteurs de vibration et de température : Ces capteurs permettent de détecter des changements dans le fonctionnement des composants critiques du système de convoyage, tels que les moteurs et les courroies. Une augmentation de ces paramètres peut indiquer un dysfonctionnement, permettant à l’équipe d’intervenir immédiatement.
- Analyse prédictive : Il est possible de prédire avec une précision remarquable quand une panne est susceptible de se produire. Cette approche, appelée maintenance prédictive, permet d’effectuer les réparations exactement au moment où elles sont nécessaires.
- Plateformes de gestion intégrée : Ce sont des plateformes logicielles qui intègrent tous ces systèmes de surveillance en un seul endroit. Cela permet de surveiller en temps réel l’état de tous les convoyeurs et de recevoir des rapports détaillés sur leurs performances.
Réduire le temps d’inactivité dans les systèmes de convoyeurs est essentiel pour maintenir la productivité et la compétitivité dans le secteur logistique.
L’utilisation de technologies de pointe et une formation adéquate du personnel permettent de minimiser les arrêts, d’optimiser les performances et de garantir que toutes les parties du système fonctionnent comme elles le devraient.