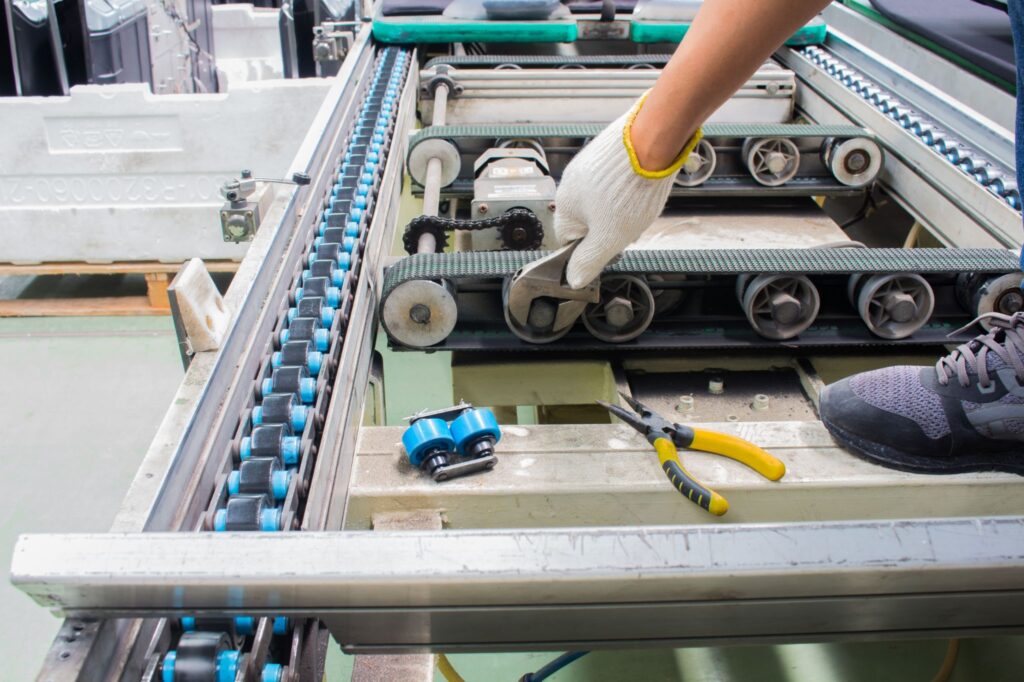
Inspection visuelle des bandes transporteuses
Temps de lecture: < 4 minutesUne inspection visuelle régulière peut être la clé pour maintenir vos bandes transporteuses en excellent état.
Voici les étapes clés pour réaliser une inspection visuelle efficace, la fréquence recommandée et les avantages de sa mise en œuvre.
Étapes clés pour réaliser une inspection visuelle efficace
- Préparation et sécurité: avant de commencer l’inspection, assurez-vous que le système est éteint et verrouillé pour éviter tout mouvement inattendu.
- Inspection de la bande: vérifiez la surface de la bande, recherchez des signes d’usure, des fissures ou des coupures.
- Vérification de la tension : assurez-vous que la bande est correctement tendue. Une tension incorrecte peut provoquer des glissements de la bande.
- Alignement: vérifiez que la bande est bien alignée, car un mauvais alignement peut entraîner une usure inégale et des dommages.
- Inspection des rouleaux et poulies : vérifiez ces éléments pour détecter tout signe d’usure ou de désalignement.
- Vérification du niveau de propreté de la bande : assurez-vous que les pièces en contact avec la bande soient propres, car la saleté et d’autres substances peuvent s’accumuler.
Fréquence recommandée pour l’inspection visuelle
La fréquence des inspections dépend de divers facteurs, tels que le type d’application, l’environnement dans lequel la bande fonctionne, la taille de la charge et la fréquence d’utilisation.
Certaines bandes fonctionnent dans des environnements plus exigeants, avec des températures extrêmes ou des produits lourds. En fonction de ces facteurs, une fréquence d’inspection plus ou moins élevée sera déterminée.
Avantages de l’inspection visuelle régulière pour la maintenance préventive
- Détection précoce des problèmes avant qu’ils ne deviennent des défaillances majeures, permettant ainsi des réparations planifiées et évitant des arrêts imprévus.
- Réduction des temps d’arrêt, ce qui se traduit par une productivité et une efficacité opérationnelle accrues.
- Économies de coûts grâce à la détection et à la résolution rapides des problèmes.
- Prolongation de la durée de vie des composants, optimisant ainsi l’investissement dans les équipements.
- Amélioration de la sécurité et réduction du risque d’accidents, garantissant un environnement de travail plus sûr pour les employés.