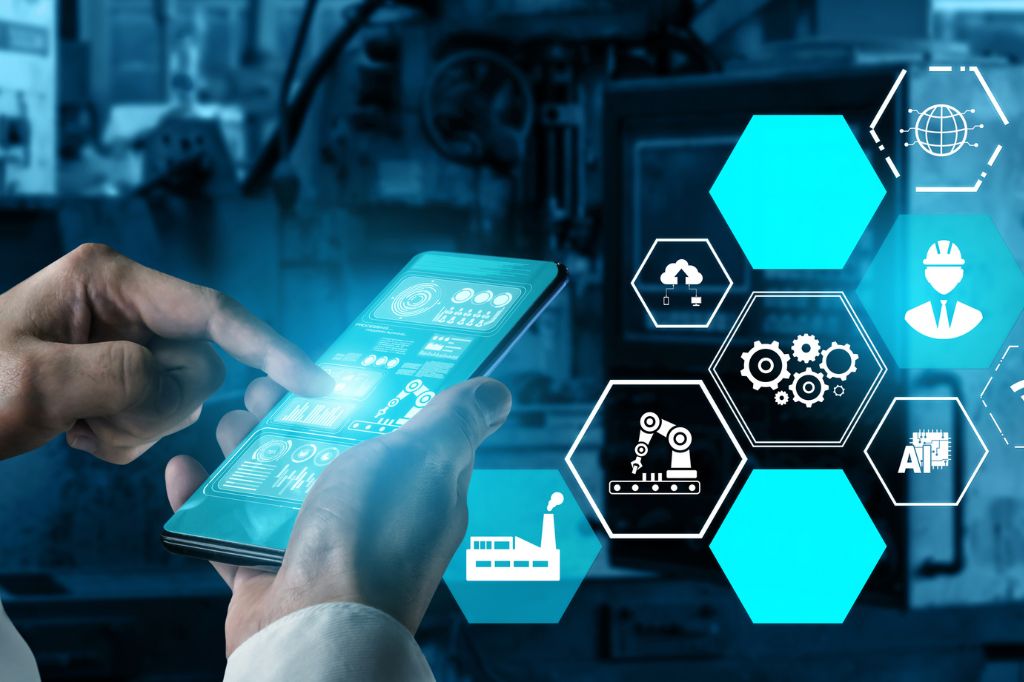
Benefits of Implementing Motorized Rollers in Industry 4.0
Reading time: < 5 minutesThe digital transformation of industry has led to the modernization of production processes through the incorporation of new technologies.
In this context, motorized rollers or Drive Rollers have become highly relevant, as they allow for more efficient automation of material transport within factories.
Unlike conventional conveyor rollers, motorized rollers have an integrated motor that allows precise control of movement, improving efficiency and flexibility in production lines.
In this article, we will explore the relationship between motorized rollers and Industry 4.0, as well as the benefits their implementation can bring to companies looking to optimize their processes and adapt to new market demands.
What is Industry 4.0 and its relationship with motorized rollers?
Industry 4.0 is based on automation, interconnectivity, and real-time data usage to improve production processes. Technologies like artificial intelligence and the Internet of Things (IoT) have revolutionized manufacturing, leading to smarter, more efficient, and adaptable factories.
Driven rollers fit perfectly into this new paradigm, as they integrate compact motors into their structure, eliminating the need for external transmission systems like chains or belts. This not only reduces the space required on production lines but also allows for quieter, more efficient operation with less maintenance.
Unlike conventional conveyor rollers, driven rollers can operate independently or together within an automated system, facilitating the implementation of smart transport lines.
Benefits of Integrating Driven Rollers into Industry 4.0
The implementation of Driven Rollers in material transport systems offers great advantages for companies looking to modernize their operations. Here are the main benefits:
Greater Efficiency in Material Transport
These rollers allow for precise control of speed and product flow on the production line, optimizing transfer time and reducing the need for manual intervention.
Additionally, their ability to operate in synchronization improves space management and prevents buildup or delays in production processes.
Reduction of Energy Consumption
Drive Rollers reduce energy consumption since they include low-energy motors with optimized efficiency, decreasing operating costs and contributing to the company’s sustainability.
Reduced Maintenance and Increased Lifespan
Driven rollers require less maintenance than traditional chain or belt-driven systems, as they eliminate unnecessary mechanical friction and wear. Their compact, sealed design protects the motor from dirt and dust, extending its lifespan and reducing the risk of unexpected failures.
Greater Flexibility and Adaptability
Drive Rollers can be adjusted to different production configurations without the need for major modifications to the infrastructure.
Their ability to operate in modular systems makes it easy to adapt to new market demands, allowing companies to quickly respond to changes in production without compromising system efficiency.
Integration with Automated Systems
Thanks to their compatibility with industrial automation systems, motorized rollers can be integrated with sensors, PLCs, and management software, enabling remote and real-time control of material transport. This facilitates the implementation of strategies such as predictive maintenance and internal logistics optimization, thus improving productivity.
Quieter and Safer Operation
The chainless and beltless design makes motorized rollers quieter compared to other transport systems.
Additionally, by eliminating external mechanical components, the risks of workplace accidents are minimized, improving safety in the plant.
Ultimately, Industry 4.0 requires efficient and adaptable solutions to improve production and logistics processes. In this context, motorized rollers represent an innovative alternative that not only optimizes material transport but also contributes to cost reduction, energy savings, and improved safety in industrial plants.