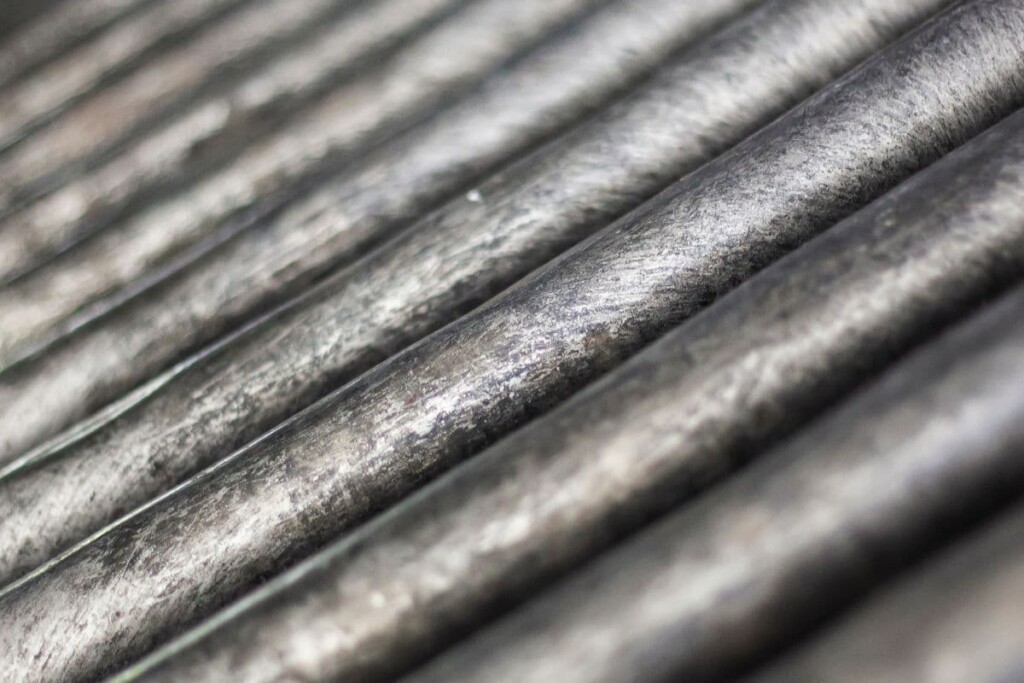
Best practices for conveyor roller installation
Reading time: < 3 minutesConveyor rollers are a key component in today’s industrial and logistics machinery. They are responsible for moving products and materials from one point to another efficiently and reliably. However, their performance largely depends on proper installation. In this article, we will detail the best practices for conveyor roller installation. We will also explain how to optimize the efficiency of belt conveyors.
How to optimize the efficiency of belt conveyors
An incorrect installation can lead not only to poor performance but also shorten the equipment’s lifespan and increase maintenance costs. Therefore, it’s crucial to follow certain guidelines to ensure the system operates as expected. Optimizing the efficiency of belt conveyors is essential to ensure an effective and cost-efficient workflow across various industrial and logistical applications. Below are some key strategies to achieve this:
Proper component selection
Start by choosing the right components for your belt conveyor. This includes selecting the appropriate conveyor belt in terms of material, width, and tensile strength, as well as the right rollers, bearings, and motors suited to the expected load and operating speed.
Preventive maintenance
Establish a solid preventive maintenance schedule. Perform regular inspections of all components, such as the belt, rollers, and motors. Lubricate critical points according to the manufacturer’s recommendations and replace any worn or damaged parts immediately. Proper maintenance will extend the life of your conveyors and prevent costly production interruptions.
Belt alignment and tension
Ensure that the conveyor belt is properly aligned and tensioned. A misaligned or loose belt can cause tracking issues and premature wear. Use automatic or manual alignment and tensioning systems as needed.
Speed control
Adjust the conveyor belt speed according to the requirements of your application. Avoid operating them at unnecessarily high speeds, as this can increase wear and energy consumption.
Load optimization
Pay attention to load distribution on the belt. Avoid overloading or underloading the conveyor, as both situations can cause premature wear and poor performance.
Monitoring and control systems
Implement monitoring and control systems to track the real-time performance of the belt conveyors. These systems can detect issues such as blockages, belt deviations, or overloads, enabling quick responses and minimizing downtime.
Incline optimization
If your belt conveyor has a significant incline, ensure it is designed and set up to handle it properly. This may include using impact rollers and retention systems to prevent the load from sliding down.
Energy efficiency
Consider energy efficiency when selecting motors and other components. Use variable speed drives and soft start systems to reduce energy consumption peaks during startup.
Staff training
Ensure that the staff operating and maintaining the belt conveyors are well-trained. Adequate knowledge of best operational and maintenance practices is crucial for maximizing efficiency and safety.
Documentation and record-keeping
Maintain a detailed record of all maintenance and repair activities, as well as any modifications or updates made to the belt conveyors. This documentation will be valuable for performance tracking and informed decision-making.
In summary, by implementing these strategies, you can maximize the productivity of your belt conveyors and achieve a more efficient workflow in your industrial or logistics environment.