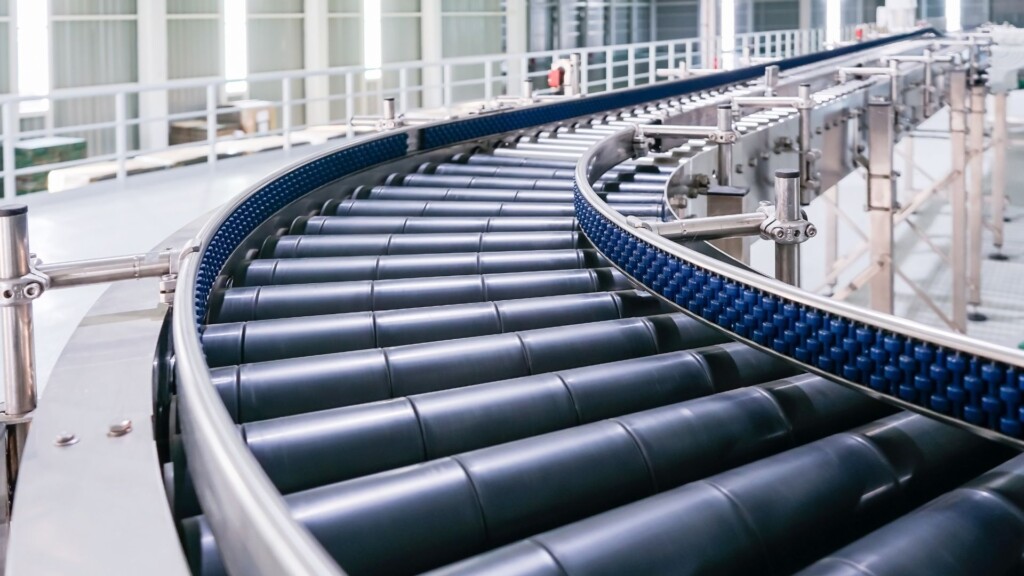
How to choose the perfect coating for your industrial rollers
Reading time: < 5 minutesIn the world of industrial manufacturing, choosing the coating for rollers is a critical decision that can significantly impact performance, durability, and operational efficiency. Industrial rollers are essential components in various applications, from material transportation to processing machinery. In this article, we will explain in detail how to choose the perfect coating for your industrial rollers, highlighting key aspects such as material knowledge, resistance to temperature and chemicals, mechanical properties, ease of cleaning, cost efficiency, and the importance of consulting with experts in the field.
Material knowledge
The first step is to understand the importance of the base material of your industrial rollers. The coating choice should complement the base material to ensure proper adhesion and optimal resistance. For example, if the rollers are made of stainless steel, it is crucial to select a coating that adheres well to this material and offers the desired properties for the specific application.
Your operations may involve a variety of materials, each with its own characteristics and challenges. The selected coating should be versatile and adaptable to different types of materials to ensure consistent performance in various working conditions. Considering compatibility with metals, plastics, or other relevant substrates is essential for making the right coating choice.
Resistance to temperature and chemicals
Temperature and exposure to chemicals can vary considerably depending on the industrial application. It is essential to assess the specific working conditions to determine the required thermal and chemical resistance for your rollers. Some applications may involve extreme temperatures, while others may be exposed to corrosive chemicals. A coating that can withstand these conditions will ensure the long-term durability and performance of your rollers.
There are specialized coatings designed to resist extreme temperatures or chemically aggressive environments. For instance, high-temperature polyurethane coatings or ceramic coatings may be viable options in environments with extreme demands. We can ensure the correct selection by carefully evaluating operational conditions and looking for coatings with specific properties for those conditions.
Mechanical properties
The mechanical properties of the coating are critical for ensuring adequate resistance to load and wear. Depending on the application, rollers may be subjected to heavy loads or constant wear due to contact with abrasive materials. Both the extended lifespan of the rollers and their durability will be secured by choosing a coating with suitable mechanical strength.
The coefficient of friction is another key aspect of the mechanical properties to consider. A coating with the right coefficient of friction can improve load transfer efficiency and minimize friction, which in turn reduces wear and increases operational efficiency.
Ease of cleaning
In environments where cleanliness and hygiene are a priority, such as the food or pharmaceutical industry, the ease of cleaning the coating is essential. Rollers must be easy to clean to prevent the buildup of residues and ensure compliance with sanitary standards. Smooth, non-porous coatings are ideal for making this task easier and maintaining a hygienic production environment.
In addition, resistance to material adherence is another factor to consider. A coating that prevents processed products or materials from sticking ensures smooth operation and reduces the need for frequent cleaning. This is especially important in applications where cross-contamination must be minimized.
Cost efficiency
While the initial cost of the coating is a factor to consider, it is important to evaluate the total cost of ownership. This includes factors such as durability, replacement frequency, and associated maintenance expenses. A more expensive but durable coating may be more cost-effective in the long run by reducing replacement and maintenance investment.
It is important to find a balance between economic value and coating performance. Some coatings may have a higher initial cost but offer significant benefits in terms of durability and operational efficiency. Evaluating the relationship between these aspects is essential for making informed decisions and optimizing return on investment.
Consultation with experts
When choosing the perfect coating for your industrial rollers, consulting with experts in the field is highly recommended. Manufacturers and specialized suppliers can provide specific guidance based on detailed knowledge of materials and industrial applications. This personalized advice ensures that the coating choice aligns perfectly with the specific needs and operational conditions of your company.
Experts can assess the unique conditions of your manufacturing process and recommend tailored solutions. This detailed evaluation ensures that the selected coating not only meets general requirements but also adapts optimally to the specific demands of your operations.