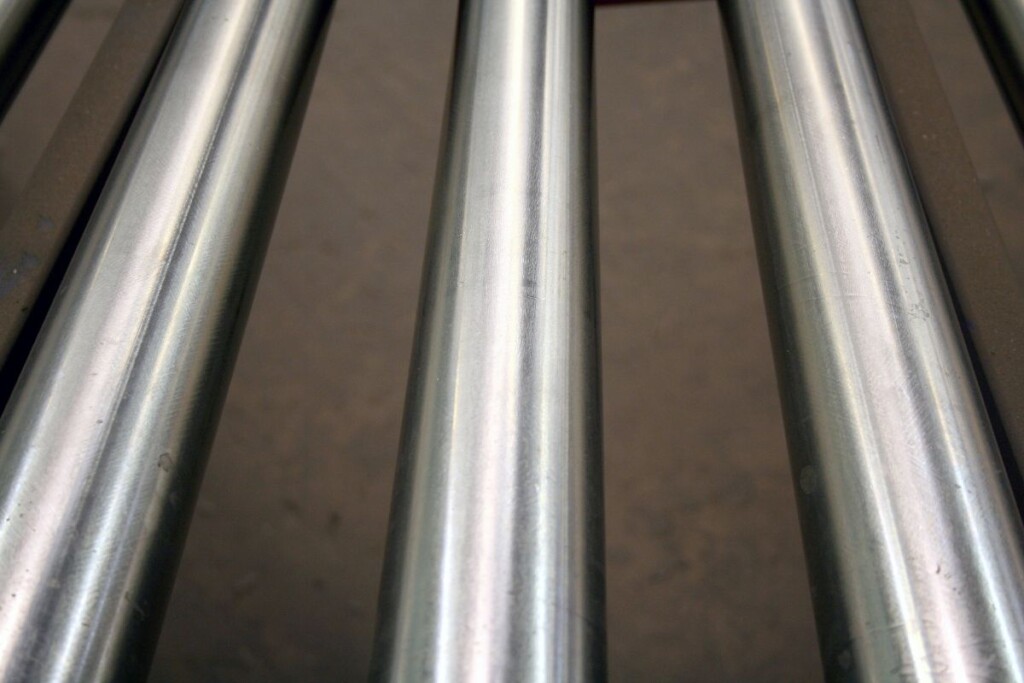
Friction reduction: Innovations in conveyor rollers
Reading time: < 4 minutesIn the world of industry and logistics, efficiency is key. Reducing friction in conveyor rollers is essential to keeping operations running smoothly and cost-effectively.
In this post, we will explore various innovations that have revolutionized the way conveyor rollers reduce friction, thereby improving productivity and extending the lifespan of the equipment.
Low friction materials
Choosing the right materials is crucial in reducing friction in conveyor rollers. Advances in material engineering have enabled the development of low-friction composites that outperform traditional materials such as carbon steel. The use of materials like Ultra High Molecular Weight Polyethylene (UHMWPE) and nylon has been shown to significantly reduce friction in rollers.
UHMWPE, for example, is known for its excellent wear resistance and low friction. This material allows products to glide smoothly over the rollers, reducing the energy required for transportation. Additionally, these materials are resistant to corrosion, increasing the lifespan of conveyor rollers in humid or corrosive environments
Optimized roller design
Another significant innovation in friction reduction for conveyor rollers is optimized design. Rollers with precisely designed profiles can minimize contact points with the transported products, thereby reducing friction. Additionally, the shape and size of the rollers can be adapted to reduce impacts on the products, which is especially important in applications involving fragile items.
Design also plays a key role in load distribution, preventing uneven wear of the rollers. A well-designed roller ensures that the load is evenly distributed, prolonging the lifespan of components and reducing friction during the process.
Smart lubrication
Lubrication has always been an essential element in reducing friction in conveyor rollers. However, innovations in smart lubrication are taking this practice to the next level. Automated lubrication systems, controlled by sensors and software, enable precise application of lubricants at critical friction points.
Smart lubrication not only reduces friction but also prevents lubricant waste and minimizes environmental impact. Additionally, these systems can be programmed to apply lubricant only when needed, reducing operational and maintenance costs.
High-efficiency bearings
Bearings play a fundamental role in reducing friction in conveyor rollers. The adoption of high-efficiency bearings, such as high-precision ball bearings and cylindrical roller bearings, has helped minimize friction at the roller support points.
These bearings are designed to withstand heavy loads while maintaining smooth and constant rotation, reducing resistance to motion. Furthermore, advanced materials and improved surface treatments extend the lifespan of bearings and reduce the need for frequent replacements.
Monitoring technology and predictive maintenance
Monitoring technology and predictive maintenance have revolutionized the way conveyor rollers are managed. Real-time sensors and monitoring systems allow operators to constantly monitor the condition of the rollers and detect potential issues before they turn into costly failures.
Predictive maintenance not only reduces unplanned downtime but also contributes to friction reduction. By quickly identifying and addressing issues such as bearing wear or lack of lubrication, further damage is avoided, and the efficiency of conveyor rollers is maintained at its peak.
As a manufacturer of conveyor rollers, we understand the importance of these innovations and are committed to providing cutting-edge solutions that help our clients reduce friction in their operations. If you’re looking to improve the efficiency of your conveyor rollers and reduce friction in your workflow, contact Eurotransis.