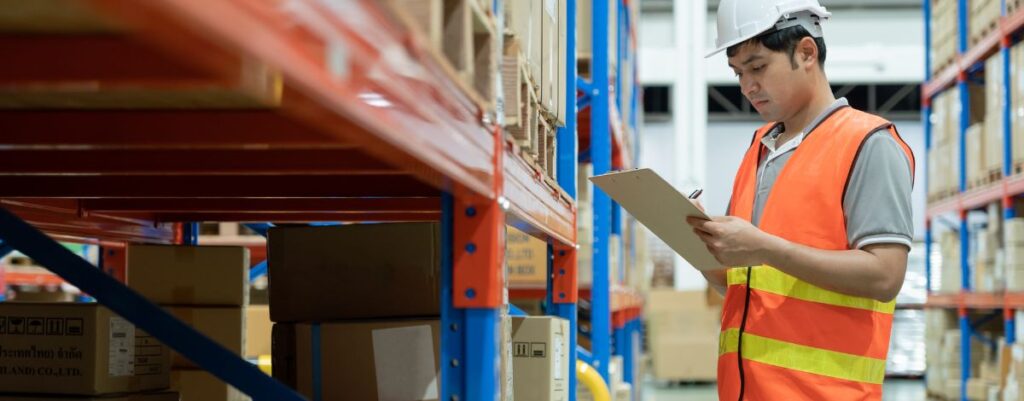
How to choose the ideal stock management model?
Reading time: < 5 minutesIf there is a concept intimately related to the efficiency of a warehouse, it is the correct management of the stock. The choice of the most optimal stock management model requires the proper evaluation of the needs of a company and for this we need to have data to analyze
In this case, the numbers we need to opt for one model or another of stock management are the storage costs referred to three fundamental points:
- Storage costs
- Order costs
- Indirect costs
Storage costs
This group includes all expenses related to the occupation of space, goods movement (machinery, rollers conveyor, belt conveyor, maintenance) supply costs and services (light, water, cleaning) controlled condition maintenance (according to the type of merchandise: temperature, humidity, etc.) half-life of the product (for perishable products), insurance, etc.
Order costs
All those related to the preparation of the order: picking, product assembly, packaging and shipping. Technical and human resources in the warehouse itself and in the administrative management, It includes that of the necessary time in the preparation of the orders and the one that will invest both the mechanical resources and the operators
Indirect costs
Are those costs related to cancellations of orders, returns or changes of products (within this aspect differentially evaluate those that are due to shipping errors or defective products / quality other than those offered).
The following points that we have to evaluate for the choice of a stock management system are:
- The demand for a product. This is an aspect or fundamental, the more demand more stock and replacement needs.
- The frequency of exposure. Storage capacity and supply by the supplier less need for stocking.
- Product half life
- Delivery time , with more delivery time more storage cost
Once with the data we can opt for the most optimal system for our business model. We show you some among which we can choose.
ABC model
This model consists of differentially managing the goods in the warehouse based on their importance (product value) and storage costs. It is really compartmentalize the warehouse into three categories: category A; most important merchandise and that require a different management from the rest. Category B; goods with high demand and reposition but average storage cost, Category C; goods that are in greater numbers but with low storage costs.
Just in time model (JIT)
This model seeks to achieve the lowest possible inventory that makes the warehouse productive and efficient. The purpose is to minimize storage costs.
It is a very dynamic model that requires two fundamental control points, 1: an extreme knowledge of the stock and location in the warehouse 2: It depends on a strong control and confidence in the ability of immediate repositioning by suppliers. This system needs to have real-time information of the warehouse stock location and exhaustive data on the delivery times of the supplier.
Wilson Model or EOQ (Economic Order Quantity)
It is based on order control so that the least possible are made including the maximum number of items in them. It is about having the minimum stock needed for daily or scheduled work until the arrival of the next order. It is a model used in small and medium-sized companies that, due to their activity, know their inventory needs in the warehouse for the assembly of equipment, machinery or facilities. This system is common in subsidiaries or regular suppliers of other companies.
The choice of an ideal stock management model seeks to optimize the quantity or number of units of a product with the minimum associated costs. We can choose several stock management systems, to decide which one to implement in our company .We must previously analyze the costs of our warehouse related to: product demand, replacement time (by supplier), its replacement rate, the costs associated with storage and indirect costs (cancellations, returns and exchanges).