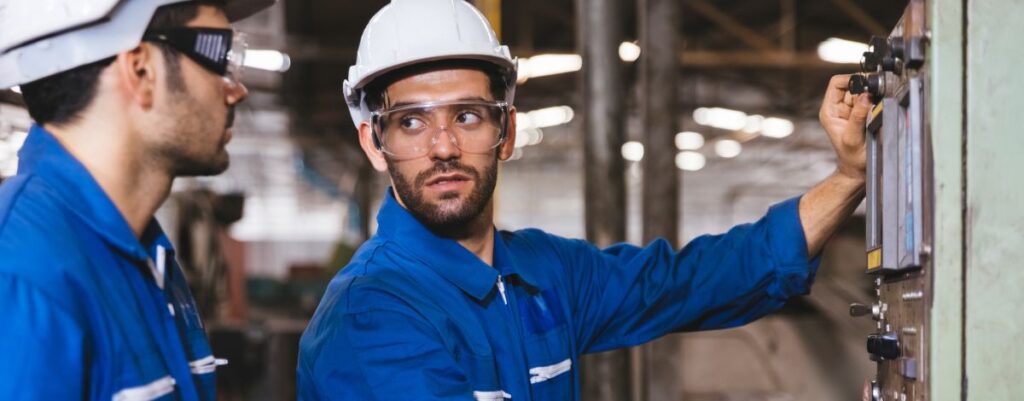
The importance of preventive maintenance in industry
Reading time: < 4 minutesFor the industry, a good maintenance of machines, mechanisms and electric systems, and also control devices, it is fundamental for its optimal performance.
Along the history, the industrial maintenance it has happened to be done only when there was a breakdown in the machines or devices, to join the integral management of productive system as one more element to manage within all the factors or departments (production, costs, risks evaluation)
Preventive industry maintenance encompasses differents elements: electric systems, industrial machines (storage, production, distribution and in the industry transport): control systems, automatisms and tools to computerize management.
What are the caracteristics and the advantages of a preventive industry maintenance?
- Industrial maintenance must be programmed
Maintenance work must be planned and managed within a specific program of actions in wich the interventions have to be carried out and clearly defined, the periodicity and corrective measures if problems are detected.
- Preventive maintenance join the equipment security
A correct equipment and machinery maintenance allow to safely work, minimizing the possibilities of dangerous failures. Preventive maintenance program must be partly integrated into occupational risks preventive management.
- Increase production performance
The minimization of posible failures that cause the production to stop or the underutilization of some production line, is one of the objectifs of the preventive maintenancce in industry.
The availability of an installation during the production is a key point to control for a adecuate final performance.
- Reliability of the productive process
The maintenance of any machines or mechanism of period form, will allow to increase its useful life and performance. The periodic rewiews and the evaluation and analysis in each one of them of a state of the machinery, allows: on the one hand, to decrease the number of serious failures; and the other hand, analyze the causes a failure to prevent in the future that failure (predictive maintenance).
- Preventive maintenance allows identify improvement points
During the maintenance tasks, you can identify the most critical points that require updating or improvement in the design or in the materials; identify processes in the production that require special attention; etc.
That allows the readjustment of the planification and of the control points of preventive maintenance, both to increase its efieciency as to reach a reduction of maintenance costs.
Elements to control in preventive maintenance
As we said at the beginning, preventive maintenance must be programmed and planified according to certain points of performance.
- Machines maintenance and revision.
- Revision, replacement and repair of mobile elements (rollers, conveyor belts).
- Conduits maintenance and revision.
- Control systems revision (probes, scales, meters, detectors)
- Evaluation of product quality as an indicator of the condition of the machine.
- Electric systems revision.
- Security system revision.
- Automatisms revision. Automatized control system (software and hardware).
The ultimate purpose of preventive maintenance is to minimize or avoid failures that lead to a loss of production or safety problems. For a company or an industry is paramount for it’s maximum performance to carry out a correct management of preventive maintenance in a integrated way to production and economic management.